Geração, Transmissão e Distribuição
de Energia Elétrica .: |
Tipo SST 5 - Secagem de Transformador Realizada por Furnas
|
Tratamento e Secagem de Parte Ativa de Transformadores Energizados
.: |
Luiz Fernando de Amorim Cintra Vidal (1)
Sérgio Roberto Claro Mendes (2) |
Resumo
|
Este trabalho tem como objetivo mostrar e comparar
os diversos processos de secagem da parte ativa de transformadores
utilizados no Departamento de Produção Rio - DRR.O,
de Furnas Centrais Elétricas SA.
A crescente preocupação com a confiabilidade dos transformadores
de potência do sistema de Furnas, principalmente com a nova
regulamentação do setor elétrico Brasileiro,
em que se penaliza as paralisações para manutenção
dos equipamentos, levou a Divisão de Manutenção
Eletromecânica Rio a desenvolver e implantar novas tecnologias
de monitoramento, controle e acompanhamento das condições
operativas dos transformadores.
Dentro desta concepção, buscou-se desenvolver uma metodologia
para realizar a secagem com o transformador energizado, de forma segura
e eficiente.
Analisaremos os tratamentos efetuados com o transformador desenergizado
e as modernas técnicas de secagem com o equipamento energizado,
mantendo a confiabilidade e a disponibilidade do sistema elétrico,
a diminuição dos desligamentos e das manobra dos equipamentos
das subestações, o aumento da economicidade e a redução
dos custos e a minimização dos riscos de agressão
ao meio ambiente.
Descreveremos as etapas de estudos de planejamento e desenvolvimento
quanto a aplicabilidade dos processos, segurança, custos e
resultados diretos e indiretos.
Com a adoção de uma metodologia moderna de manutenção
foi possível obter uma redução de 87% dos homens-horas
e de 100% no tempo de indisponibilidade para a manutenção
de secagem dos transformadores.
|
 |
(1) Luiz Fernando de Amorim Cintra Vidal – Engenheiro mecânico,
formado em 1975 pela Universidade Católica de Petrópolis
– UCP. Chefe da Divisão de Manutenção Eletromecânica
do Departamento de Produção Rio de Furnas Centrais Elétricas
SA.
(2) Sergio Roberto Claro Mendes – Engenheiro Eletricista, formado
em 1983 pela Universidade Gama Filho – UGF. Engenheiro da Divisão
de Manutenção Eletromecânica do Departamento de
Produção Rio de Furnas Centrais Elétricas SA.
|
 |
1- Histórico – A situação em 2000
|
Furnas Centrais Elétricas
SA atua em uma área que envolve as Regiões Sul, Sudeste,
Centro-Oeste e o Distrito Federal, que concentra 67% da produção
industrial brasileira, e onde vivem 50% da população
brasileira, consumindo 66% da energia produzida no País.
Possuindo uma capacidade instalada de 9.290 MW, gerada em 10 usinas
hidrelétricas e 2 termelétricas, seu sistema compreende
42 subestações com uma capacidade de transformação
de 81.191 MVA, interligadas por 17.640 km de linhas de transmissão,
nas tensões de 138 até 765 kV AC e 600 kV DC.
O Departamento de Produção Rio possui 68 transformadores
com tensão maior de 138KV.
Ao longo da vida dos transformadores, existe a possibilidade de
penetração de umidade no óleo que migra para
o papel do enrolamento, reduzindo a rigidez dielétrica do
óleo isolante e a tensão de ruptura do papel, acelerando
seu envelhecimento térmico tendo como produto formação
de água, reduzindo a capacidade dielétrica da isolação
e por conseqüência, levando o equipamento a falha.
O controle da umidade da isolação sólida é
fundamental para se minimizar a degradação da celulose,
obtendo-se um significativo aumento da vida útil do transformador.
O acompanhamento periódico do teor de água ( ppm )
é fundamental para se determinar a necessidade de secagem
da isolação.
A tabela a seguir mostra as recomendações para secagem
de transformador, em operação, conforme o nível
de tensão.
|
Nível de Tensão |
PPM do Óleo |
£ 230 kV |
40 ppm |
> 230 kV |
30 ppm |
|
 |
2 Processos de Secagem da Isolação
|
2.1 Transformador Desenergizado |
O processo mais usual para secagem da isolação do transformador,
devido a eficácia, é a utilização de ciclos
de óleo quente – vácuo.
Esse processo consiste em aplicar vácuo menor ou igual a 1
Torr no transformador sem óleo por, no mínimo, 24 horas,
colocar óleo a 55º C no transformador até cobrir
a parte ativa e a isolação dos cabos e circular o óleo
a 90ºC (saída do transformador), mantendo-o por 24 a 48
horas. Após esse período, retirar rapidamente o óleo
a 90º C, injetando ar seco pela parte superior do transformador.
( Ver esquemático)
Devem ser aplicados tantos ciclos quanto necessários para a
secagem do transformador.
|

Esquemático |
 |
2.1.1 Controle e Determinação do Processo de Secagem
|
No início de cada ciclo, antes
do enchimento do transformador deve ser retirada amostra de óleo
isolante para determinar o teor de água. Este valor deve estar
na ordem de 10 ppm.
Procedimento idêntico é adotado durante a circulação
de óleo, quando o óleo atinge a temperatura de 90º
C e após 24 ou 48 horas de circulação.
Pela comparação desses dois últimos resultados
de teor de água é verificada a eficiência do processo
e determinado o seu término |

|
2.1.2 Considerações |
Para a realização do tratamento, é necessária
a substituição do transformador a ser tratado pelo reserva,
acarretando indisponibilidade do sistema elétrico, custos de
pessoal e riscos para o equipamento.
Toda operação dos ciclos de óleo quente –
vácuo é assistida por pessoal técnico envolvendo
enorme quantidade de tarefas. |
TAREFAS
1. Início
2. Instalação máquina secadora de ar ou garrafa
de ar
3. Medição DEW POINT na secadora
4. Normalização máquina purificadora/resistor
aquecimento
5. Instalação (bomba de vácuo)
6 . Amostra de óleo tanque principal
7. Retirada óleo tanque principal
8. Desmontar radiadores e flangear tanque principal
9. Retirada do óleo do LTC
10. Interligar LTC/tanque principal - inspeção/medição
LTC
11. Cobrir autotransformador com lona (isolar termicamente)
12. Enchimento tanque principal
13. Circulação óleo quente (96 h) a 98oC (10
vezes o volume do transformador)
14. Dreno do tanque principal com alta vazão
15. Vácuo no mínimo 24 h (< 1 TORR)
16. Quebrar vácuo
17. Medição DEW POINT após 24 h
18. Vácuo no mínimo 24 h (<1 TORR)
19. Quebrar vácuo com ar seco
20. Medição DEW POINT após 24 h
21. Repouso óleo no tanque de armazenamento
22. Transferência óleo T1 -> T2
23. Transferência óleo T2 -> T1
24. Vácuo no mínimo 24 h <1 TORR - tanque principal
25. Enchimento tanque principal 55o/retirada amostra/óleo
26. Circular óleo tanque principal p/48 h a 90o/amostra óleo
27. Retirada amostra óleo saída tanque principal após
24 e 48 h
28. Retirar óleo tanque principal
29. Circular óleo no tanque T1 por 24h a 55oC
30. Vácuo no autotransformador por 24 h <1 TORR
31. Amostra óleo de T1 a 55oC
32. Quebrar vácuo com ar seco
33. Medir DEW POINT
34. Instalar radiadores e abrir válvulas
35. Vácuo de 6 h <1 TORR
36. Enchimento final tanque principal a 55oC
37. Retirada amostra óleo tanque principal
|

|
2.2 Transformador Energizado Utilizando Cartuchos Absorvedores |
Os cartuchos absorvedores garantem que na saída da máquina
a umidade do óleo seja menor que 10 ppm, não liberam
água quando saturados, não interferem no acompanhamento
de gases dissolvidos, não prejudicando o diagnóstico
de defeitos incipientes por cromatografia, nem removem inibidores
de oxidação porventura presentes no óleo.
Para que seja execução da secagem com o transformador
energizado, foram analisados os seguintes aspectos:
|

|
2.2.1 Segurança |
Os quatro cartuchos são trocados simultaneamente
de forma segura e rápida. |
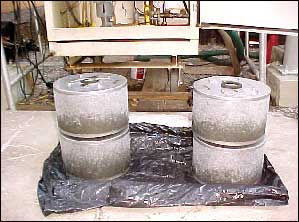
Cartuchos filtrantes da máquina |

|
O óleo é retirado pela parte inferior do transformador
e retorna pelo tanque de expansão, numa vazão de 1130
l/h, garantindo baixa turbulência de óleo na parte ativa
do equipamento evitando cargas estáticas e interferência
na refrigeração do transformador. |

|
A máquina é projetada para operação
desassistida, as mangueiras são providas de solenoides em suas
extremidades ligadas ao painel principal de controle. Caso ocorra
perda de fluxo, por exemplo devido a vazamento nas mangueiras, a máquina
é desligada e as solenoides interrompem o fluxo de óleo. |

Vista Geral da Máquina 
Conexão da mangueira com solenóide no Tanque de Expansão

Conexão da mangueira com solenóide parte inferior
|
A mangueira principal é envolvida por outra
mangueira para que em caso de vazamento, o óleo seja coletado
numa bandeja no fundo da máquina, atuando uma boia de nível,
sinalizando a ocorrência e evitando um acidente ambiental. |

Mangueiras principais envolvidas por mangueiras
espiraladas para coletar óleo em caso de vazamento

Entrada e Saída das mangueiras principais da máquina

Bandeja coletora de óleo e alarme de nível de óleo
|
A eliminação de bolhas de ar na circulação
do óleo, é garantida pelos procedimentos de evacuação
do ar da máquina e mangueiras pela bomba de vácuo conectada
no sistema de filtragem. |

Evacuação de bolhas de ar do sistema |