Geração, Transmissão e Distribuição
de Energia Elétrica .: |
Tipo SST 5 - Secagem de Transformador Realizada por Furnas
|
2.2.2 Controle e Determinação do processo de Secagem
|
O cálculo da quantidade
de água retirada por dia é feito pela subtração
da umidade no óleo ( ppm ) que entra na máquina pela
umidade do óleo ( ppm ) que sai da máquina multiplicada
pela taxa de fluxo em horas de operação.Considera-se
que o ensaio de umidade do óleo na entrada é na condição
de regime do transfomador e com carregamento e temperatura constante.
Exemplo:
|
[20 ppm(entrada) – 5 ppm(saída)
= 15 ppm] * 5 gpm * 60 min |
= |
0,1 gl de água |
 |
|
 |
1.000.0000 ppm |
|
dia |
|
Ensaios periódicos
de teor de umidade no óleo na entrada e saída do sistema,
é usado para determinar a necessidade da troca dos cartuchos
.Um conjunto de cartuchos tem capacidade de retirar no mínimo
2,6 l de água dissolvida no óleo.A umidade na saída
começará a aumentar à medida que o cartucho
atinge sua capacidade de retenção de água.Os
cartuchos não liberam a umidade de volta para o óleo
mas o processo não será mais eficiente até
sua troca.
|
 |
Tratamento efetuado na Subestação do Grajaú:
|
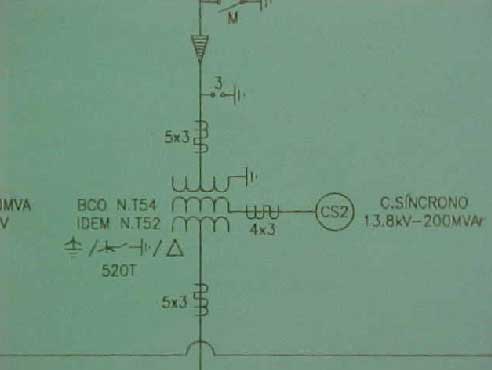
|
Nº de série: 55818 Ano de fabricação:
1975
Volume de óleo: 75.000 Litros
Elevação de temperatura do:
- Óleo: 55ºC
- Enrolamento: 55 ºC
Tensão 500/138/13.8 kV
|
 |
Condições iniciais:
40 ppm
Temperatura do óleo isolante 52 º C
% de umidade no papel ( por massa ) - 2,8 %
- Entrada do filtro – 39 ppm
Saída do filtro – 6 ppm
Temperatura do óleo - 52ºC
Observação: Filtros novos
- Após tratamento de 364.632L de óleo
Entrada do filtro – 19 ppm
Saída do filtro – 16 ppm
Temperatura do óleo - 50ºC
- Após tratamento de 396.960 litros de óleo
Entrada do filtro - 27 ppm
Saída do filtro - 27 ppm
Temperatura do óleo - 48ºC
- Entrada do filtro – 40 ppm
Saída do filtro – 7 ppm
Temperatura do óleo - 68ºC
Observação: Filtros novos
- Após tratamento de 725.506 litros de óleo
Entrada do filtro – 42 ppm
Saída do filtro – 42 ppm
Temperatura do óleo - 67ºC
|
Condições iniciais : 40 ppm Temp. óleo
52ºC - 2,8%
Condições finais : 42 ppm Temp. óleo 67ºC
- 2,0% |

|
 |
2.3 Transformador Energizado Utilizando Filtros de Coalescência
|
Os filtros de coalescência são
utilizados para a separação das moléculas de
água dissolvidas no óleo isolante, através da
associação com um conjunto de vácuo e placas
refrigerantes.
O óleo retirado da parte inferior do transformador, é
bombeado com baixa vazão, similar ao processo de filtros absorventes,
e passado pelo filtro de coalescência, que separa as moléculas
de água, que são agregadas as placas refrigerantes e
acumuladas durante um período de 168 horas. Após este
período, o processo totalmente automatizado, desliga o bombeamento
de óleo e aquece as placas refrigerantes, sendo a água
coletada em um frasco volumétrico.
O sistema é dotado de um medidor digital on-line de teor de
água no óleo para acompanhamento da eficiência
do processo. A quantidade de água é medida no frasco,
descartada, e o processo poderá ser reiniciado para tantos
ciclos de secagem que as condições do equipamento necessitar.
Na instalação da máquina e execução
da secagem, são efetuados os mesmos procedimentos de segurança
e controle do processo, ao da secagem com cartuchos absorvedores.
( itens 2.2.2 e 2.2.3 ) |

Vista do Equipamento |

|
2.3.1 Considerações |
Transformador Desenergizado
No processo de secagem utilizando-se ciclos de óleo quente-vácuo,
o equipamento a ser tratado é substituído pelo reserva
através de desligamento. É necessário pessoal
técnico durante todo o serviço, envolvidos numa enorme
quantidade de tarefas. Transformador Energizado
O funcionamento da máquina de forma desassistida não
gerou nenhuma ocorrência comprometendo o transformador ou processo
de secagem.
Os custos são significativamente menores, redução
de mais de 50%, sendo que no método dos filtros de coalescência,
a redução é maior ainda pois os mesmos não
são trocados durante o processo.
O método demonstrou ser seguro e confiável para operação
com transformador energizado, efetivamente retirou umidade da parte
ativa, atendendo as necessidades da manutenção e mantendo
a disponibilidade do sistema.
|

|
3 Conclusão |
O trabalho de secagem da parte ativa de transformadores é um
trabalho desenvolvido pela DMER.O/DRR.O em parceria com fabricantes
de equipamentos de secagem e outros órgãos de Furnas,
particularmente a Divisão de Equipamentos de Transformação
– DETF.O do Departamento de Equipamentos de Alta Tensão
– DAT.O.
Iniciado em 2000, com o desenvolvimento de máquinas especiais
de tratamento e secagem da parte ativa, este processo tem obtido um
alto índice de aceitação por parte dos nossos
clientes.
A realização das manutenções de secagem
dos transformadores com os equipamentos energizados, que nos processos
convencionais era necessário desligar o equipamento por um
período longo, que dependia do grau de umidade do transformador
e do tipo de processo utilizado, reduziu a zero a quantidade de desligamentos
para esta finalidade.
O não desligamento dos transformadores contribuiu para o aumento
da confiabilidade e da disponibilidade dos equipamentos do setor elétrico.
Contribuiu também para a diminuição do número
de manobras dos equipamentos das subestações, por não
necessitar isolar os transformadores, diminuindo a possibilidade de
falha em outros equipamentos associados.
Por não ser necessário o manuseio do óleo isolante
entre o transformador e o tanque, ou para outro local, minimiza-se
o risco de agressão ao meio ambiente, ocasionado por vazamento
de óleo isolante.
As vantagens acima relacionadas demonstram que esta metodologia trouxe
uma economia substancial, com ganhos de disponibilidade e confiabilidade
elevados e com uma qualidade do serviço inegável.
|

|
4 Bibliografia |
1. Manual
Técnico de Campo – Tratamento de Transformadores
no campo – Furnas Centrais Elétricas S.A. – Rio
de Janeiro - 2001
2. Vidal, Luiz Fernando de Amorim Cintra; Mendes, Sergio Roberto
Claro – Secagem da Parte Ativa com Transformador Energizado
– Trabalho publicado no 2º Encontro Técnico de
Equipamentos de Transformação de Furnas Centrais Elétricas
- Rio de Janeiro – 2001
|