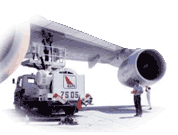
|
Additive
Injector - 600 Series |
The Model 600 - The
Industry Standard For Truck Mounted Additive Injection |
The 600 Series system offers single or multiple additive injection
at flow rates typically found in aviation refuelers, hydrant
systems, heating oil delivery trucks, and water treatment vehicles.
The unique positive displacement driver responds precisely to
changes in product volume even at very low flow rates. Like
all Hammonds injectors, the 600 dispenses precise quantities
of additive at an almost continuous rate, eliminating the "slugging"
effect typically found in meter pulsed injectors. The additive
is injected just ahead of the driver, providing complete, consistent
additive mixture blending.
|
Completely Self-Contained
Units |
The efficient Hammonds fluid powered motor "borrows"
just enough energy from the flowing product line to do the job.
No need for electricity, air or pressurized additive lines.
|
Totally
Unassisted Injection |
Complete, passive operation means they automatically operate
when the rest of the system operates. No need to remember to
turn the injector on or off. It if is connected to a system,
it "remembers" when to run, how much to run and when
to stop. The operator has nothing to remember, nothing to adjust,
nothing to forget.
|
Meters
And Pulsars No Longer Required |
Because our fluid motor acts as bot a source of control and
power, additional meters and pulsars are not required.
|
Installation
Is Simple And Economical |
With a Hammonds system, there is only one simple mechanical
pipe connection. No wiring in hazardous conditions, no additional
equipment on other parts of the system to install, no concrete
work, or costly site engineering to lay out pipes, conduit,
pumps and skids. In most cases, a system can be ordered that
will "drop in" to your existing piping, requiring
very little on-site preparation.
|
Guaranteed
Precision Blending |
Unlike some systems that inject large slugs into the product
at metered intervals, the Hammonds injector continuously dispenses
a precise measured rate of additive that matches the existing
flow rate. There are no gaps in the injection process. Since
the injection point usually upstream of the fluid motor, thorough
blending of product and additive is achieved.
|
Specifications |
Number of Additives
One (1) standard
Two (2) optional
Injection Ratios
One (1) additive
0-1300 PPM with standard 1S Head
0-3600 PPM with optional 2L Heads
Two (2) additives
0-2000 PPM each additive with 1L Heads
Minimum Injection Ratio: 1 PPM
Normal Operating Range: 0-300 GPM
Minimum Product Flow Rate:10 GPM
Maximum Product Temperature: 0-250°F
Maximum Product Line Pressure:100 PSI (PSI varies with
injection ratio - consult factory for requirements greater
than those specified)
Product Viscosities: to 10,000 SSU
Additive Supply Requirements: Flooded suction
Products Handled: Ideal for low viscosity materials
with some lubricating qualities
Fluid Connections:
Product: 3" Victaulic Connections
Additive: ¾" FMNPT standard
Materials of Construction:
Fluid motor: Anodized Aluminum
Additive injector: All wetted parts 300 series Stainless Steel
Elastomers: Buna-N, PTFE, Viton
|
On/Off
Operation |
Additives can be turned on or off at pump or with an optional
remote control panel with sight flow indicators.
|
Additive
Supply |
Flooded suction is preferred, moderate suction lift is acceptable.
|
Ratio
Stability at Low Flows |
Even if startup and shutdown flow rates are below stated minimums,
unit can be calibrated to maintain overall ratios. The system
will maintain ratio for total product throughput.
|
Location |
No restrictions on mounting adjacent to turns, valves or other
pipe fittings.
|
Back
Pressure |
Pressure and flow rates are not significantly affected.
Differential pressure at 75 GPM = 3 PSI
|
Mounting
Attitude |
Units can be installed in vertical or horizontal lines. The
output shaft on the fluid driver should be arranged in a horizontal
position.
|
Standard
Equipment |
- 600 series fluid motor
- All anodized cast aluminum housing
- 3" victaulic connections
- Hammonds 1S single, small fluid end injector pump
- All Stainless Steel wetted parts
- 3-way On/Off/Calibrate valve
- Adjustable "while running" calibration
- PTFE elastomers
- Stainless Steel check valves
- Stainless Steel injector manifold
- Calibration port
- Built-in injection point with check valve
- Instruction manual with calibration charts
- Graduated calibration bottle
- White acrylic enamel paint
- Factory loop tested to customers specifications
|
Optional Equipment
|
- Custom product line fittings
- -3" flanges
- -3", 4" 150# RF ANSI flanges
- Suction Strainer
- Suction sight flow indicator
- Suction on/off ball valve, Stainless Steel
- Remote control panel
- Remote electronic controls
- All Stainless Steel construction
- PTFE coated internals
- Epoxy coated internals
- Custom additive tanks
- Weatherproof enclosures
- Multiple additive capability
|